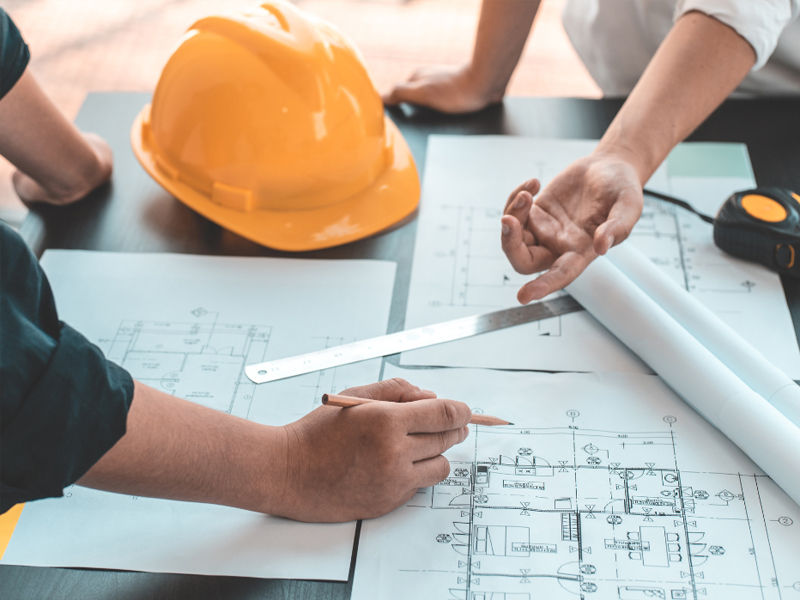
Pre-planning is crucial for insulation success, yet it’s often an overlooked step in many construction projects. Contractors who integrate insulation considerations early in the design phase can avoid common pitfalls that lead to inefficiencies, delays, and extra costs. This post outlines important strategies for ensuring insulation is planned properly from the start, ultimately leading to better results and long-term energy efficiency.
1. Integrating Insulation into the Design Phase
A common challenge in construction is that insulation is often considered too late in the process. Architects and designers may focus heavily on the aesthetics of a building, unintentionally neglecting essential space for insulation in key areas like roofs and walls. By the time insulation contractors are brought in, changes can be costly and time-consuming.
To avoid these issues, it's important to:
Plan for adequate insulation space during the design phase, ensuring that structural components like roofs and walls can accommodate the necessary R-values.
Make sure the design doesn’t call for insulation sizes or materials that are not readily available in the market, which can lead to delays.
Collaborate early with insulation companies near you to identify potential design flaws that may affect the building’s energy efficiency.
Early integration of these factors can ensure that insulation needs are met without costly changes during construction.
2. Planning Around Structural Elements
Structural elements, such as wood framing, have a significant impact on how effective insulation will be. If a building is designed with framing that is too small to allow for proper insulation thickness, the energy efficiency of the building will suffer. For example, using 2x8 framing instead of 2x12 can limit insulation depth and reduce thermal performance.
Contractors should work closely with design teams to ensure that structural elements are planned with insulation in mind, balancing the need for strength with the right space for energy-efficient materials.
3. Collaboration with Architects and Designers
Collaboration between contractors, architects, and insulation contractors is essential to ensure that insulation is properly planned. One common design oversight is placing ductwork in unconditioned attic spaces. This often leads to significant energy losses because ducts are exposed to extreme temperatures—hot in summer and cold in winter—which forces HVAC systems to work harder.
For projects requiring attic ductwork, spray insulation companies can offer tailored solutions, like spray foam, to ensure maximum energy efficiency by sealing gaps and preventing heat loss.
4. Cost Implications and Mistakes to Avoid
Skipping insulation pre-planning can lead to budget overruns and poor long-term energy efficiency. Some cost-effective strategies include:
Consulting with insulation professionals early in the project to avoid common mistakes, like underestimating the space needed for insulation.
Ensuring that all areas, including hard-to-reach spaces like attics and basements, are planned with proper insulation in mind.
Using insulation materials that meet the building’s long-term needs and consider potential future renovations or expansions.
5. Essential Tools and Technologies
Using the right tools and technologies is critical to ensuring a successful insulation project. Today, advanced tools like spray foam applicators and insulation software allow contractors to achieve better results in less time. Contractors should work with partners who have access to these tools and can provide the most efficient, cost-effective solutions.
Choose the Right Insulation Partner for Your Project
Incorporating insulation into the early design and planning stages is essential for creating energy-efficient, cost-effective buildings. By taking these steps, contractors can avoid common pitfalls, ensure that their projects meet energy standards, and deliver better results for their clients.
When it comes to finding the right insulation contractor for your projects, SoundSeals Insulation has the tools, techniques, and expertise to get the job done efficiently and effectively, at the right price. Thanks to our volume purchasing power, we are able to offer competitive pricing without sacrificing quality. We continuously upgrade our skills through ongoing training, ensuring that we are always up-to-date with the latest insulation standards.
We proudly service the Almaguin, Barrie, Bracebridge, Collingwood, Gravenhurst, Haliburton, Huntsville, Huronia, Midland, Muskoka, Parry Sound, Penetang, Wasaga Beach, and the Near North regions.
Contact us today at 705-746-0066, email info@soundsealsinsulation.com, or visit www.soundsealsinsulation.com to learn how we can support your next project from start to finish.